
Making a Difference
We are dedicated to providing our customers with solutions that enable economic, environmental, and safety benefits.
Improving Efficiency
Our solutions allow operators to reduce costs, reach deeper depths and improve the efficiency of operations.
Our Customers
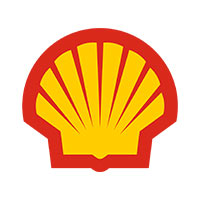
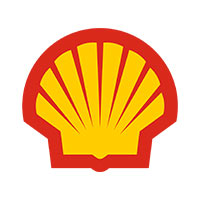


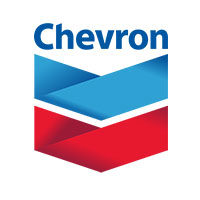
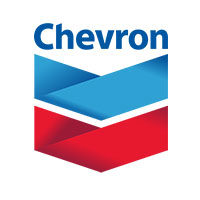
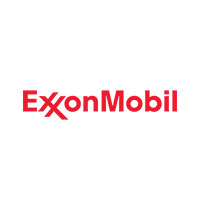
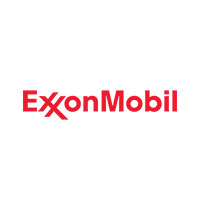
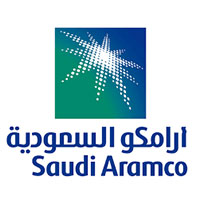
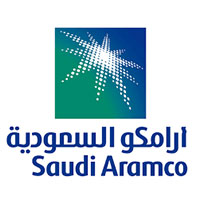
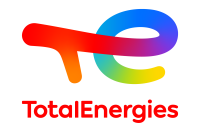
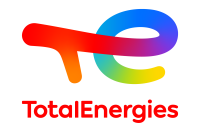
One Source. Many Solutions.
NCS Multistage manufactures solutions for all stages of energy production.
We provide the most innovative, tested, and reliable solutions for the most demanding applications.
Setting Standards
Our experience and love for innovation converge in a consistent effort to set new industry standards.
Wells Traced
Screenouts Managed
Bn